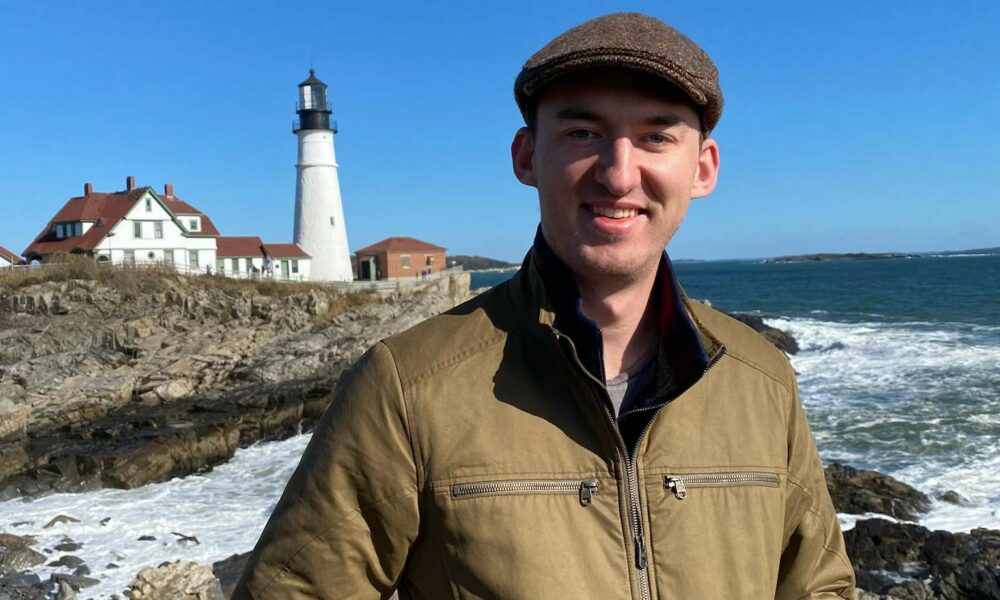
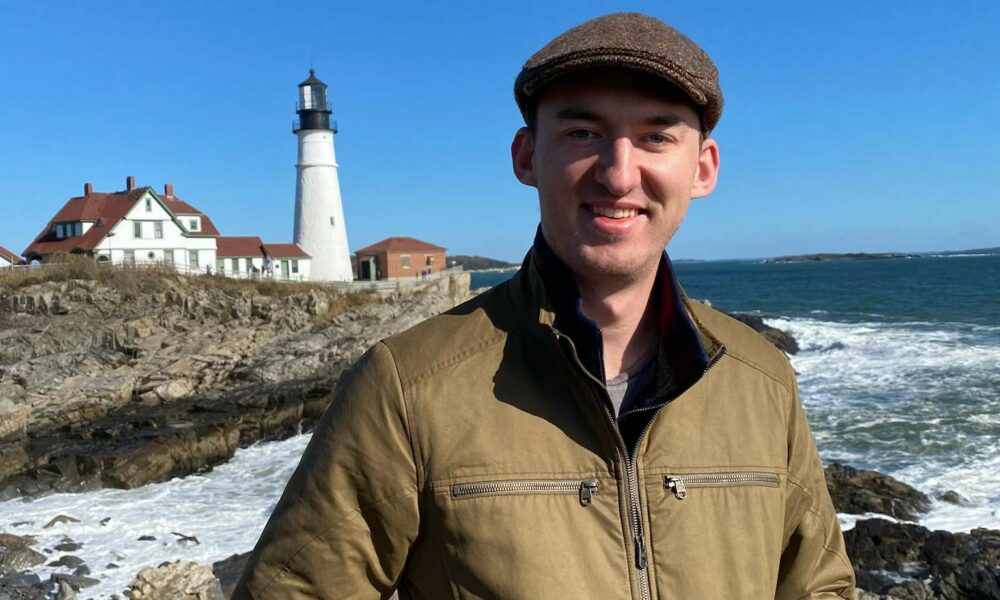
Today we’d like to introduce you to Josh Harp.
Hi Josh, we appreciate you taking the time to share your story with us today. Where does your story begin?
Ever since I was a little kid, I was completely obsessed with boats of all kinds, but especially wooden boats. I had posters and thrift store paintings of sailboats on my wall. Then, I took a wood shop at North Kansas City High School. I was lucky enough to have an amazing teacher in Steven Wagner, who was encouraging and flexible enough to let me work on other projects that weren’t for a grade but just because I wanted to keep making things. This was when I started seriously thinking I would one day build a wooden boat.
After high school, I studied mechanical engineering at UMKC in KC. I didn’t want to be an engineer, but I was good in school and figured engineering was as close to designing/working with my hands as possible. In my sophomore year, I interned at Olssen Associates doing mechanical drawings for new development apartments and offices, which broke me. I could not handle sitting at a computer that long. I needed to work with my hands. One day after work, I researched wooden boat builders worldwide. I figured somewhere there had to be someone doing this stuff for a living, and I would figure out how they were doing it. I listed about 25 companies worldwide and sent them the same email. The gist was, “How did you get into this industry, and what do I need to be doing to point myself in the right direction?” Of the 25, about 10 of them got back to me, and all had the same response: I needed to show them that I had a vested interest in the craft and that I already had some skills and then used that to look for an apprenticeship.
From there, I decided that the best way to do both was to build a boat and document the whole process. Since I lived in the Midwest and had limited space to accomplish this, I decided it was best to build a canoe. I started building the canoe and then got to a stage where I needed a copious amount of epoxy. The only business in the KC area that sold it was a place called KC Sailing. I drove out there on a snowy February day to buy a few gallons of epoxy, and the guy working there started talking to me and asking questions about what I was working on because it was pretty uncommon for someone to purchase epoxy in such quantities. I gave him my schpeal about wanting to become a wooden boat builder, and he told me that if I needed help on the canoe project, I should call him because he was interested.
About 2 weeks later, I called him and asked for an internship/job at the shop. I went out there for one of the goofier interviews of my life and was hired on the spot by some of my closest friends, Jon and Sarah Duffendack. I spent the remainder of my time in college working at the shop every weekend and spending my nights steadily working on the canoe in my garage whenever I could spare a few hours. Working on boats had become everything I had hoped it would be, and although I was finishing my engineering degree, I had no intention of using it. I planned to work at the shop full-time after graduation.
However, the shop didn’t have the workload to support me for 40 hours a week, and it was April of my senior year, and I was panicking. A professor at UMKC, Dr. Travis Fields, somehow heard through the grapevine that my boat plan had fallen through. He offered me a job in his research lab and said he would fund my master’s degree. I liked the guy; his lab was very hands-on, so I tried it. About halfway through the master’s degree, I finally finished my first canoe. It only took me 3.5 years and probably close to 600 hours of work to finish. Its maiden voyage on Smithville Lake was the happiest and most satisfied I had ever felt up until that point, and that feeling reignited the flame. Just because my boat plans had fallen through in KC doesn’t mean I couldn’t make it work elsewhere. I had some family and friends in St. Paul/Minneapolis, MN, and knew the wooden boat community up there was strong. So I took some of the photos of my work at KC Sailing and the photos of my canoe and sent an email to a few shops up there asking for an interview. St. Paul shipwrights owner Mark Sauer gave me a call and scheduled an interview with me.
A few weeks later, I drove up, and after talking with him and the crew for about an hour, I was hired on the spot. It was official. I was moving to St Paul, Minnesota. I then graduated with my master’s in mechanical engineering in December of 2019 and moved to St Paul in January of 2020. It was negative 12 degrees the day I moved in with my older brother and his wife, and I couldn’t have been more excited. Then I started my new job, restoring old wooden boats, and it was just amazing. I was learning so much every day and getting to work with my hands. Then, 2 months later, COVID hit, and the world shut down. I was furloughed indefinitely and am now trapped in a cold city with my brother and his wife to keep me company. We eventually made it back to work, but the experience had given me time to evaluate the longevity of my time in Minnesota. Between the extreme cold and the higher cost of living compared to KC, it just wasn’t working, and to be honest, I mostly just missed my friends and family. So, almost a year later, I moved back to KC and took a full-time engineering position at UMKC. I worked there for about a year and a half, saving up money, and when the time was right, I decided to go for it and start building boats on my own.
During my time in MN, I cultivated a real love of the old Chris Craft runabouts, specifically from the 1920s-40s era, as that was one of many of our restorations. While up there, I thought that if I started building canoes in the style of those runabouts, there had to be a real market for that because there is so much nostalgia among wood boat owners. I decided to make that my brand identity, took all that knowledge I’d gained in the year in MN, and poured it into a canoe. Using the exact paint, stains, fabrics, hardware, and everything I could think of to make this canoe look like a Chris Craft Runabout. I was nervous about how people would take it, though, as either paying homage to those boats or ripping them off. I then drove to Port Townsend, Washington, with my canoe in tow on a 31-hour road trip to the annual wooden boat festival to find out. The reception could not have been better, and I was overjoyed. I sold the boat to a gentleman I met at the show and made some great contacts. I am now in my second year of business and in the process of building another Chris Craft-inspired canoe, and I hope to keep doing it for years to come.
Alright, so let’s dig a little deeper into the story. Has it been an easy path overall, and if not, what challenges have you had to overcome?
It has not. Wooden boat building is so niche that it is difficult to find places to learn how to do it; most of it is discovered by doing. I bought as many books on various kinds of building methods as possible. I watched every conceivable YouTube video before getting professional training in a real shop. Also, finding your client base can take time, even once you have cultivated the skills to do it. Most boat shows have limited space, and companies that have been to the show in previous years have priority. when you’re a newcomer and a one-person shop, convincing the show coordinators to give you space can be difficult. Also, trying to convince your family that it is a good idea to quit your engineering job to start building high-priced wooden boats can be a difficult conversation to have.
Let’s switch gears a bit and talk business. What should we know?
Harp Boat Shop specializes in constructing strip-plank wooden canoes, kayaks, and row boats. We do commissioned work as well as in-house designs. As far as I know, we are the only company in the world creating paddle craft in the likeness of the runabout motorboats of the 1920s-40s. Everything from the wood to the paint, fabric, stain, varnish, hardware, etc., is as authentic to those runabouts as possible. These boats take several months to build and are constructed entirely by hand. No part of the process is automated, and our attention to detail and quality sets us apart. The company’s founding idea was making functional art and ensuring that our boats weren’t just something pretty to look at. For this reason, every boat is laminated in fiberglass on both the inside and outside of the hull. The fiberglass turns transparent upon lamination, so you get the beauty of the wood, but the strength and abrasion resistance of the fiberglass makes our boats strong as well as gorgeous.
We’d love to hear about your fond memories from growing up.
My favorite childhood memory is of any day getting up to no good with all my brothers. We are still extremely close to this day, and I see them several times a week. They even help me work on the boats occasionally.
Contact Info:
- Website: www.harpboatshop.com
- Instagram: https://www.instagram.com/harpboatshop/
- Facebook: https://www.facebook.com/profile.php?id=100088011384780
- Youtube: https://www.youtube.com/@harpboatshop
- Other: https://www.tiktok.com/@harpboatshop?lang=en
Image Credits
Josh Harp